How process simulation with Cardanit transformed a leading wire manufacturer’s production efficiency

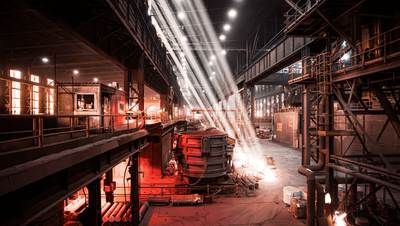
-
Organization: University of Trieste
-
Design challenge: Identify the most efficient setup for a new unwinding system, significantly reduce operational bottlenecks and boost plant flexibility.
-
Benefits:
Validate production performance across different system configurationsTest system responsiveness under varying conditions and identify operational bottlenecksHelp evaluate changes in automation strategies before physical implementation
In today’s competitive industrial landscape, optimizing production workflows before physical implementation is critical to reducing downtime, improving efficiency, and making smart investment decisions. In this success story, discover how a leading manufacturer of cold rolled flat and drawn wires leveraged Cardanit’s powerful process simulation tools to redesign a key phase of its manufacturing operations.
A recent graduate in Mechanical Engineering of the University of Trieste used Cardanit’s powerful business process simulation feature to write his dissertation which ended up helping the manufacturing company make its choice. By modeling and simulating two alternative automation scenarios for its new unwinding system, the company identified the most efficient setup, significantly reducing operational bottlenecks and boosting plant flexibility. Using BPMN modeling and BPSim simulation in Cardanit, the team evaluated complex interdependencies between eight production lines, tested real-time configurations, and made data-driven decisions - all before installing a single machine.
The ContextIntroduction of process simulation in manufacturing
In an industry under constant pressure to innovate, companies in the manufacturing sector must pursue technological advancement to remain competitive. Simone Puppis, a recent graduate with a Master’s degree in Mechanical Engineering, managed to introduce the usage of process simulation within a manufacturing company. Thanks to his work, a leading manufacturer of cold rolled flat and drawn wires with low and medium carbon content, launched a major initiative to modernize its operations. The objective: increase production efficiency and workplace safety through automation.
The design and simulation of an automatic unwinding system for a new production plant was at the core of this effort. The goal was to replace the manual coil separation process with a mechanized one, optimizing the production flow from wire drawing to storage. Business Process Management (BPM) played a key role from the very beginning, enabling Simone to clearly map out operations, identify constraints, and explore different system configurations.
The ChallengeOptimizating the automatic production flow
The team faced a precise but complex engineering challenge: how to design an automatic unwinding station that could integrate seamlessly with eight independent wire drawing lines. The transition from a manual to an automated workflow introduced interdependencies and resource-sharing complications that couldn’t be left to guesswork. This change was intended to significantly increase production efficiency and improve workplace safety. This operational stage is crucial because, after the drawing process, the product is wound onto a coil, from which it must be separated for final delivery to the warehouse and, ultimately, the customer.
Objectives:
- Replace manual coil separation with an automated unwinding system.
- Simulate production scenarios to validate the efficiency of proposed designs.
- Optimize resource allocation and reduce operational downtime.
Key challenges:
- Ensuring smooth, continuous operation across all eight lines.
- Managing shared resources and process interdependencies.
- Making accurate predictions before construction and capital expenditure.
The SolutionProcess simulation finds the break point
Choosing Cardanit as the modeling and simulation tool turned out to be a game-changer. The manufacturer needed a platform that would enable modeling complex production processes with clarity and simulate them with accuracy. Cardanit offered the perfect combination of visual BPMN 2.0 modeling, BPSim-based simulation capabilities, and an intuitive user experience that allowed the team to hit the ground running.
Simone began by creating a digital representation of the production process. Key stages such as coil strapping, 90-degree vertical rotation, and final transfer to the storage area were modeled as Service and User Tasks. These workflows, previously managed manually by operators, now had to be represented in a way that was both faithful to reality and functionally precise. Cardanit’s auto-layout and color customization features made it easy to organize complex diagrams, making them easier to interpret, share, and refine collaboratively.
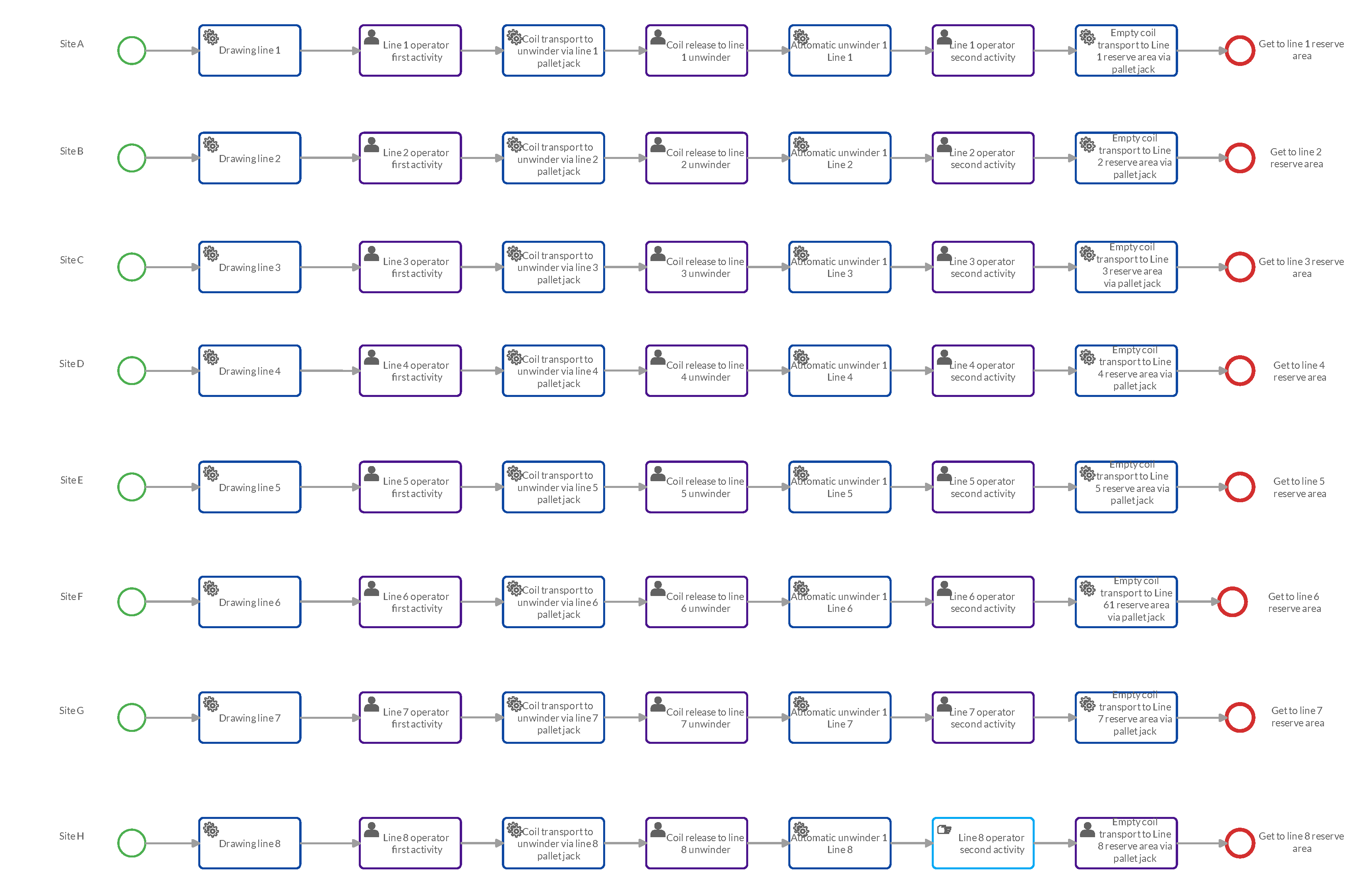
Once the model was established, next was simulation. This is where Cardanit’s full potential really came to life. Simone used real data on task durations and introduced various resources like “Unwinder” and “Transpallet” (representing electric pallet trucks). Then he simulated two different plant configurations:
- Scenario 1: One unwinder resource serving all eight production lines.
- Scenario 2: Two unwinders splitting the workload, each responsible for four lines.
The last crucial element is the unwinder cycle time, the key parameter for optimization. As the machine is still in design, this value is unknown; thus, simulations aimed to identify a threshold cycle time to guide the choice of scenario.
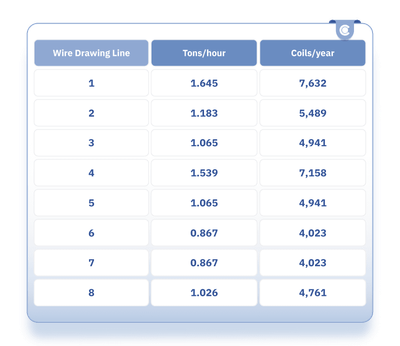
By modifying the unwinder cycle times in each simulation, he observed how different thresholds impacted resource efficiency and production continuity. With just one unwinder, the system operated efficiently only up to a certain cycle time - beyond that, wait time increased significantly. Introducing a second unwinder allowed the system to maintain continuous operations over a broader range of cycle times, increasing overall flexibility and reducing the risk of bottlenecks.
One of the key takeaways was how simulation allowed defining a “break point” - a threshold where performance started to deteriorate. This insight would have been difficult to uncover through traditional planning. With Cardanit, it’s no longer a guesswork - it’s all about testing, adjusting, and validating, all within a virtual environment.
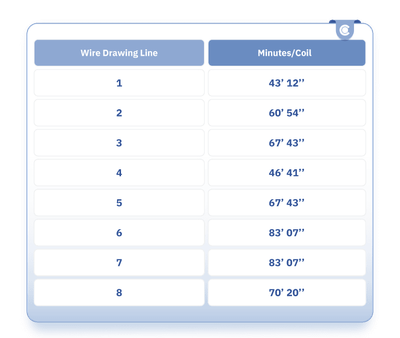
The collaborative features also played a role. Different team members - engineers, analysts, planners - could all access and contribute to the same model in real time. And when a design iteration needed review, they simply turned to version history to compare changes and track improvements.
Generating reports was just as easy. After each simulation, Cardanit provided detailed performance metrics used in stakeholder discussions and final design evaluations. What once took days of manual calculations was reduced to minutes, and with far greater accuracy.
Ultimately, Cardanit became more than a modeling tool. It became a strategic partner in the decision-making process. Also thanks to version history, it gave a safe, data-rich environment to experiment, learn, and improve, paving the way for a more efficient and forward-thinking manufacturing system.
The BenefitsProcess simulation's crucial role before physical implementation
Cardanit's BPMN and BPSim tools enabled the project team to gain valuable insights before committing to hardware investments.
Key features and their impact:
Identified bottlenecks, optimized resource allocation, tested thresholds, and validated production performance across different system configurations.
Enabled data-driven decision-making with detailed performance metrics.
Shared the models with all the stakeholders enabled iterations and changes in real time.
Tracked iterations of the design process to support continuous improvement.
Cardanit’s simulation features allowed us to virtually test our entire production redesign. It gave us confidence in our investment strategy and provided data we could trust.
Simulation focus:
- Task durations based on measured data and coil production capacities.
- Wait times and efficiency thresholds were identified through varying unwinder cycle times.
- Realistic resource modeling, including electric pallet trucks (Transpallet).
- Evaluated process continuity, resource saturation, and waiting times in different plant layouts.
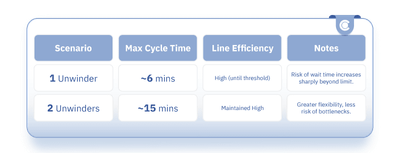
Outcome comparison table
Estimated impact:
- Up to 40% reduction in downtime with dual unwinder configuration.
- 100% continuous operation in most simulations under both setups (until threshold).
- Improved planning accuracy and faster design iterations.
- Increased throughput with optimized line usage and fewer disruptions.
Final considerations
Cardanit played a crucial role in helping the team evaluate automation strategies before physical implementation. The simulation capabilities were not just supplementary, they were central to the project's success. Through iterative simulations, the team could test system responsiveness under varying conditions, fine-tune task durations, and preemptively identify operational bottlenecks.
Cardanit made process simulation accessible and impactful. It turned a complex production redesign into a data-driven success before a single machine was built.
Simulation became a form of virtual prototyping: a risk-free environment to challenge assumptions and test hypotheses. This not only reduced uncertainty but also significantly shortened the time required to reach a confident decision. The ability to visualize how the production system would behave under different configurations and parameters, before committing to capital investment, proved invaluable.
With simulation confirming that production continuity depends on unwinder cycle time, stakeholders can now make informed decisions about system architecture and capacity planning. More importantly, they can do so knowing that those decisions are based on rigorously tested data and realistic models.
Ultimately, the ability to simulate real-world performance using Cardanit has empowered the company to take a significant step forward in manufacturing innovation - maximizing efficiency while enhancing workplace safety.
Further reading
Optimizing production by mapping business processes with Cardanit
Modeling manufacturing processes with BPMN
How Process Simulation helps verify BPMN models
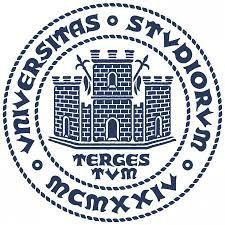
Simone is a recent graduate with a Master’s degree in Mechanical Engineering, specializing in Design and Prototyping, from the University of Trieste (2025). He wrote his thesis while being an intern at a company specialized in drawn wire production, aiming to introduce a machine to automate part of the operational process and maximize overall efficiency.
Simone is a recent graduate with a Master’s degree in Mechanical Engineering, specializing in Design and Prototyping, from the University of Trieste (2025). He wrote his thesis while being an intern at a company specialized in drawn wire production, aiming to introduce a machine to automate part of the operational process and maximize overall efficiency.
A business is only as efficient as its processes. What are you waiting to improve yours?